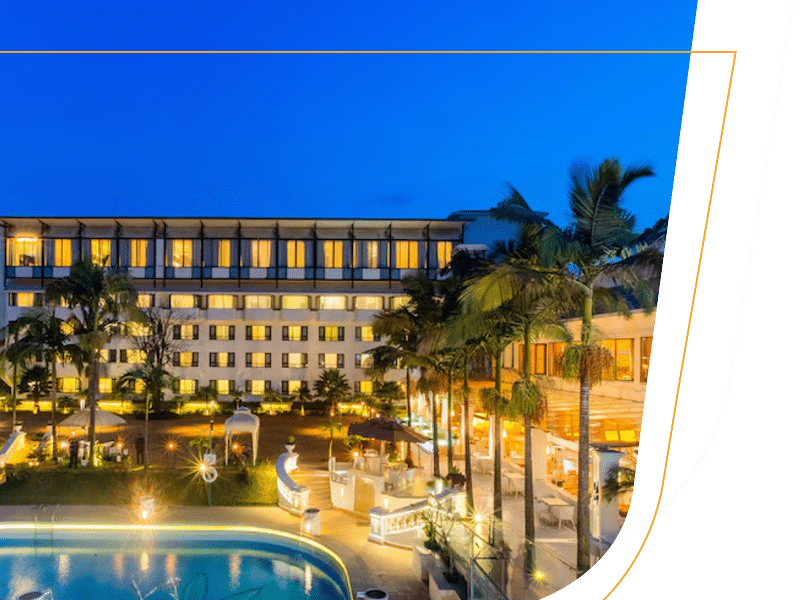
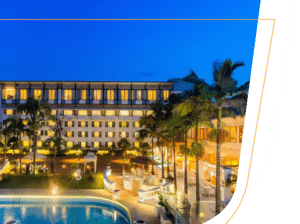
BLOG
Run-to-Fail HVAC: A Costly Risk for Hospitality in the Heat
In the hospitality industry, timing is everything. Summer marks the peak season for guest bookings, vacation travel, weddings, conferences, and events. It’s also when HVAC systems work overtime to maintain comfort and keep operations smooth. Ironically, it’s during this critical period that many hospitality facilities adopt a risky and outdated maintenance approach: run-to-fail.
While this reactive strategy may seem cost-effective at first glance, it introduces significant vulnerabilities precisely when the stakes are highest. Beyond guest discomfort, run-to-fail HVAC maintenance can lead to costly emergency rentals, long equipment lead times, contractor scarcity, increased strain on the electrical grid, and compounding revenue losses.
Let’s break down the domino effect this approach can trigger during the hottest—and busiest—months of the year.
What Is Run-to-Fail?
“Run-to-fail” is a reactive maintenance approach where HVAC systems are allowed to operate without routine service until a breakdown occurs. In industries with minimal operational sensitivity to downtime, it might be tolerable. But in hospitality, especially in summer, it’s a high-risk gamble.
The Peak-on-Peak Problem
The danger lies in the timing. Summer isn’t just peak HVAC demand, it’s also:
- Peak travel season
- Peak occupancy for hotels and resorts
- Peak event and wedding season
- Peak load on the electrical grid
When HVAC systems fail under these conditions, the consequences ripple across operations and the bottom line.
1. Contractor Scarcity: You’re Not the Only One Who Waited
When the first heatwave strikes, HVAC contractors are flooded with emergency calls. Response times stretch from hours to days. For facilities operating at or near full capacity, this downtime can result in lost revenue, unhappy guests, and damaged reputation.
And when service isn’t immediately available? You rent.
The run-to-fail approach may save maintenance costs in the short term, but failures often require emergency HVAC and generator rentals, which can dramatically increase unplanned expenses.
Emergency HVAC Rental Costs
- Small portable units (1–5 tons): $200–$600 per day
- Large rooftop units (20–100 tons): $1,000–$5,000 per day
- Portable chillers (high demand during summer):
- 25–50 ton systems: Common for medium hotels (50–150 rooms)
- 100+ ton systems: Often required for large hotels or peak capacity
Example Chiller Rental Rates:
Chiller Size |
Daily Rate |
Weekly Rate |
Monthly Rate |
10–25 ton |
$250–$500 |
$750–$1,500 |
$2,000–$4,000 |
50 ton |
$500–$1,000 |
$1,000–$2,500 |
$3,500–$6,000 |
100+ ton |
$750–$1,500 |
$2,000–$4,500 |
$5,000–$12,000+ |
Delivery and installation fees can add another $1,000 to $5,000 depending on site complexity.
2. Grid Stress: Your Run-to-Fail Practice Isn’t Isolated
Poorly maintained HVAC systems consume more energy. Dirty filters, clogged coils, and refrigerant leaks force systems to overwork, increasing the building’s energy demand. In summer, when thousands of buildings do the same, it adds intense pressure on the grid.
Consequences include:
- Local brownouts or blackouts
- Utility demand charges and peak pricing penalties
- Power surges that damage sensitive systems
Generators become your backup—but they’re not free.
Example Generator Rental Costs:
Generator Size | Daily Rate | Weekly Rate | Monthly Rate |
100 kW | $450 | $1,200 | $3,500 |
200 kW | $500 | $1,500 | $4,000 |
Typical hotel power demand:
- Small hotel (50–100 rooms): 150–300 kW
- Mid-size hotel (100–250 rooms): 300–800 kW
- Large hotel (250–500+ rooms): 800–2,000+ kW
Generator maintenance is just as critical; failure there can jeopardize business continuity during a power outage.
3. Reputation Risk: HVAC Isn’t a Luxury - It’s a Necessity
In hospitality, guest perception is everything. A sweltering lobby, stuffy room, or overheated ballroom leads to:
- Negative online reviews
- Lost bookings or canceled events
- Heat-stressed staff and poor morale
And the financial impact extends beyond inconvenience.
The Real Cost of Lost Revenue
Some studies estimate 1–3% of annual room revenue is lost due to HVAC failures and guest compensation. For a 100-room hotel with $10 million in annual revenue, that’s $100,000–$300,000 per year—from comped rooms, relocation, and reputation repair.
Additionally, HVAC-related leaks can cause slip-and-fall injuries, exposing properties to legal claims and fees.
A Smarter Strategy: Schedule Maintenance Before You Need It
Here’s how to break the run-to-fail cycle:
- Schedule preseason tune-ups (spring or early fall) before contractor demand spikes
- Implement HVAC asset tracking to monitor equipment age, performance, and service history
- Use energy management systems to detect inefficiencies and predict failures
- Establish seasonal service agreements with guaranteed response times and preferred pricing
Final Thoughts: Pay Now or Pay (Much) More Later
Run-to-fail might appear budget-friendly—until it isn’t. Factor in emergency equipment rentals, peak utility charges, extended outages due to parts shortages, legal risks, and guest loss, and the true cost of reactive maintenance becomes clear.
If just 10% of the estimated 65,000 hotels in the U.S. incurred $10,000/year in rental costs, that’s $65 million per year—and that’s before factoring in lost revenue.
Summer will always be a high-stakes season. The question is whether your facility’s HVAC strategy is ready for it—or is just waiting to fail.
Want to ensure your property is peak-season ready?
At Crete United, we help hospitality operators move from reactive to proactive HVAC strategies that reduce downtime, control costs, and keep guests cool—even when the grid is under stress. Contact us today to schedule a seasonal system audit.