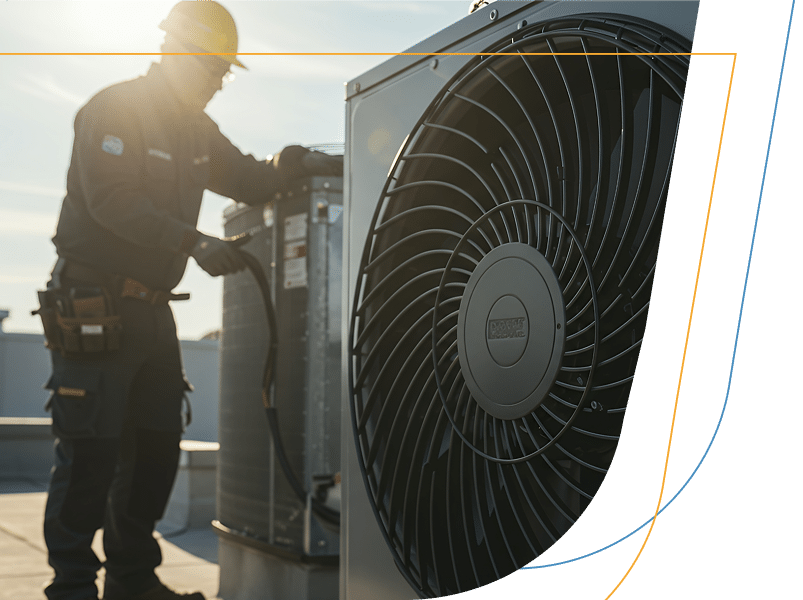
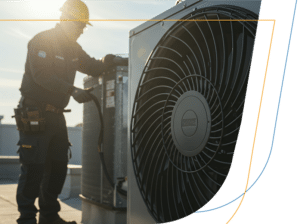
BLOG
Key HVAC Start-Up Checks for Commercial Buildings
4/16/25
Preparing HVAC systems for spring startup is essential to ensure reliable performance during the peak cooling loads of summer. Depending on geography, cooling equipment may have sat idle for quite some time, while air-handling equipment has likely been working hard all winter. Now is the time to be diligent with inspections and maintenance activities that go far beyond simply cleaning coils and lubricating moving parts.
A Spring Start-Up Checklist for commercial HVAC systems ensures smooth operation, energy efficiency, and optimal indoor air quality as the system transitions from heating to cooling. Here are the top 10 steps to make sure it happens in your facility:
- Inspect & Clean Air Filters – Replace or clean filters to improve airflow and indoor air quality. Utilize the proper efficiency filter to meet your space requirements. For systems with multi-stage filtration, ensure the most efficient pre-filter, mid-stage(s), and/or final stage filters are being utilized and replaced appropriately.
- Check Thermostat & Control Settings – Verify proper thermostat operation and recalibrate if necessary. Adjust setpoints for cooling season efficiency, put manual overrides back to their original settings, and make sure space temperature settings are adjusted to reduce equipment runtime during unoccupied periods.
- Inspect & Clean Condenser & Evaporator Coils – Remove dirt, debris, and buildup to improve heat transfer. Check for coil damage or corrosion, and make sure there is adequate space around units for proper airflow.
- Check Refrigerant Levels & Inspect for Leaks – Ensure refrigerant charge meets manufacturer specifications. Detect and repair any leaks to prevent efficiency loss.
- Inspect Belts, Pulleys & Bearings – Look for wear, cracks, or looseness in belts. Lubricate bearings to reduce friction and prevent overheating.
- Test Electrical Connections & Components – The continuous alternating flow of electrons causes vibration to occur in system components, leading to heat, harmonics, and loose connections. Tighten loose connections to prevent short circuits and inspect relays, capacitors, and contactors for wear.
- Verify & Clean Drain Lines & Pans – Clear any clogs to prevent water damage and mold growth. Check drain pans for rust or leaks. Look for and correct any temporary fixes and ensure all associated plumbing components are in proper condition.
- Test & Calibrate Economizers & Dampers – Ensure dampers open/close properly and respond to control signals to optimize fresh air intake. Clean and lubricate moving parts for smooth operation and ensure proper return and outside air mix levels.
- Inspect Ductwork & Vents – Look for leaks, blockages, or insulation damage. Ensure vents are open and unobstructed for proper airflow.
- Test System Performance & Safety Controls – Run the system to check for unusual noises, vibrations, or inefficiencies. Check for communication failures, test sequences of operation, and ensure safeties such as high-pressure cutouts and freeze protection function correctly.
It’s important to remember that seasonal start-up should not be limited to mechanical lubrication and coil cleaning. Commercial HVAC systems can be very complex, so a deeper, more comprehensive evaluation is needed to ensure upstream and downstream equipment and controls are properly communicating and working together per design. By completing the critical task of thoroughly inspecting HVAC controls, electrical safety, and plumbing components, your system will remain operational and perform efficiently all season long, significantly mitigating unexpected critical equipment failures.